Is Industrial Real Estate Running Out of Love for Tilt-up Concrete?
Tilt-up concrete buildings are dominant in the industrial real estate market for good reasons. They provide a durable wall system that simultaneously creates a watertight enclosure. Structurally efficient, their walls can support the roof without needing steel columns around the perimeter. These tall, textured walls also lend a substantial and austere appearance. Tilt-up checks many boxes for a price that’s hard to beat.
But will tilt-up buildings continue to meet the demands of Class A industrial space?
A Changing Market
The manufacturing and logistics industries are increasingly incorporating technology and automation into their processes, overseen by workers with greater skill. These advancements are raising the expectations for industrial buildings to provide clean, controlled, and comfortable environments. Buildings must also manage the rising risks of natural disasters and high temperatures, driving requirements for thermal insulation, air quality, and resilience. Investors and regulators are also keeping ESG performance front and center, with a focus on decarbonizing real estate.
These trends have created new expectations for building performance that may call to question the preeminence of tilt-up buildings.
- Resilience. Tilt-up buildings are not very resilient. If the roof fails in high winds, the wall panels are likely to collapse. The rigid walls perform poorly in earthquakes.
- Construction speed. The construction process for tilt-up buildings is labor-intensive and sequential. First, the floor slab is poured, which is then used to form and cast the tilt-up wall panels. Once the panels cure, they are hoisted and temporarily braced while the roof structure is constructed. Finally, a perimeter strip of the floor slab is poured to anchor the panels. Each step must wait until the previous sequence is complete, slowing down the overall construction speed.
- Floor slab quality. The floor slab – the most critical element for most industrial buildings – is poured first, when there is the least control over site conditions such as sun, rain, wind, and temperature.
- Energy efficiency. Tilt-up walls have insulation gaps at their interface with the foundation, doors, and roof. Building codes are becoming less tolerant of these gaps in the thermal envelope.
- Residual value. Tilt-up buildings require considerable effort to repurpose or demolish. The roof insulation is difficult to salvage, and the best option for the walls is to down-cycle them as crushed aggregate. When divesting, tilt-up buildings may be a liability.
- Wellness. Air quality and thermal comfort are compromised by lower performing enclosure systems. It’s common to omit insulation entirely adjacent to dock doors, where it is vulnerable to damage. This leaves workers exposed to cold walls in the winter and hot walls in the summer.
Despite these performance issues, tilt-up will continue to be a suitable solution for many buildings. However, companies seeking Class A industrial space are likely to grow increasingly frustrated with their limitations.
Introducing Built-up Metal Buildings
What realistic alternatives are there to tilt-up construction for Class A industrial space? We can look across the pond for inspiration, where metal buildings have commanded Class A rents for over two decades. However, in Europe these metal buildings use a double metal panel system, unlike the single-panel pre-engineered metal buildings that are pervasive in North America. This approach addresses many of the performance, sequencing, and lifecycle issues associated with tilt-up buildings.
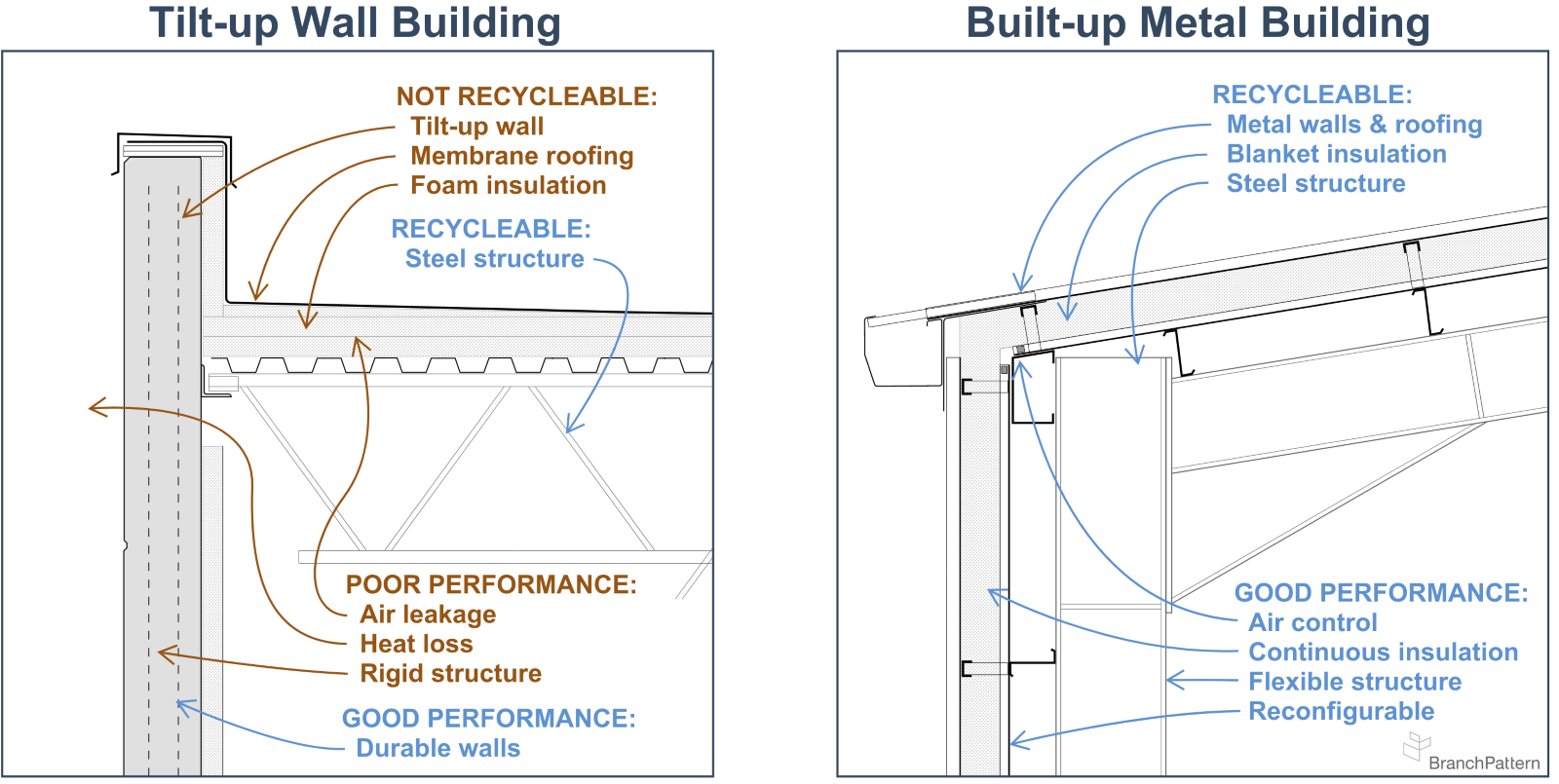
Benefits of Built-up Metal Buildings
Sometimes called a “double skin,” the enclosure system used by these buildings is also called “built-up” because the interior layer is installed first, with subsequent layers added outboard. The structure is made of prefabricated steel portal frames that are bolted together on-site. Steel girts are then installed over the frames to support the first layer of metal roof and wall panels. This inner skin is carefully sealed to provide an air, vapor, and water barrier.
A rail and bracket system are installed next, which provides a cavity for mineral wool batt insulation. The system is finished with the outer layer of roof and wall panels. Skylights are typically installed at the same time as the metal panels by using matching translucent panels.
These layers are all installed from the exterior, in contrast to single-wall systems where the insulation and air barrier are installed from inside the building. This allows work on the slab to proceed concurrently with the enclosure. It also provides easier access for workers to properly seal and insulate the system. The double wall enclosure has a vented cavity like most other high-performance wall systems, offering excellent durability, water management, and indoor air quality.
How is this different than using insulated metal panels? Unlike insulated metal panel systems, built-up metal buildings are assembled layer by layer on site. This makes the materials easy to separate later, promoting reuse and recycling of metal panels and insulation. Disassembly and a vented cavity are two distinguishing performance benefits of built-up metal buildings over IMPs.
Market Barriers
Despite their advantages, built-up metal buildings have not gained widespread adoption in North America. While cost plays a role, the larger issues are innovation risk and aversion to change. Creating open dialog with team members can provide the necessary feedback and participation to limit disruption. Here are key considerations for stakeholders in the value chain:
- Developers & Investors. To manage innovation risk, visit existing built-up buildings and identify experts to better understand the system (for example, CA Group in the UK). Collaborate with energy modelers, enclosure consultants, and life cycle assessment professionals to validate claims of energy efficiency, comfort, and embodied carbon savings. Study the potential impacts on insurance. Identify a trusted building user to anticipate any tenant concerns with occupying a metal building.
- Structural Engineers. Validate claims regarding resilience under high winds and earthquakes. Learn how built-up metal buildings differ from pre-engineered metal buildings and research fabricators’ portal moment frame capabilities. Resources are available from SteelConstruction.info.
- Architects. Built-up metal building detailing is simpler than single-wall metal buildings, but it is also very different. Excellent resources are available from the Metal Cladding & Roofing Manufacturers Association covering, for example, Detailing and, Daylighting. Specify air leakage testing and water spray testing requirements for a ‘first install’ corner of roof and wall. Lifecycle assessment professionals can also help communicate the value of built-up metal buildings.
- Builders & Manufacturers. Anticipate quality and safety risks given this is a new enclosure type. Detailing liner panels with sealants and tapes is skilled work and differs from typical metal panel installation. Liner panels may not support workers in the event of a fall. Investigate vertically integrated contracting, where manufacturers certify the installer and inspect work.
- Realtors. Built-up metal buildings can differentiate properties because they offer improved conditions for tenants. However, the single-wall metal buildings that are currently in the marketplace are often Class B or even Class C, creating a marketing liability. Seek evidence and testimonials from European counterparts to correctly value this class of building. Highlight benefits such as lower utility costs, excellent daylighting, and flexibility for additions and renovations. There are also more options for architectural expression and creativity with the façade because it is not constrained by the roof structure.
- Tenants. Tour a built-up metal building to identify opportunities and risks associated with a different building solution. For instance, consider if walls need protection from equipment or if increased daylight will reduce accidents. Will better indoor environments reduce worker turnover? Estimate utility bill savings.
Who will lead the transition to built-up metal buildings?
The shift to higher-performing industrial buildings will be driven by demand and competition. Tenants who require more resilient, occupant-centered buildings will push for innovation. However, most tenants will only demand improved buildings after experiencing their benefits firsthand. Developers are more likely to lead innovation as a tactic to gain competitive advantage in both leasing and capital markets. Sustainability differentiates otherwise similar products.
Developers are also well-positioned to navigate innovation risks. In this context, tenants and architects play supporting roles in smoothing project delivery. Success depends on an integrated team and a clear articulation of the purpose and benefits of built-up metal buildings. To summarize, we have provided a summary of those benefits.
Compared to a tilt-up wall building, built-up metal buildings:
- Are easier to heat and cool for worker comfort, reducing operational emissions.
- Have greater residual value due to adaptability and ease of disassembly.
- Allow the building slab to be poured in a dry, conditioned environment.
- Reduce cement use, lowering up-front emissions.
- Feature larger skylights, improving safety while saving energy.
- Perform better in extreme weather and earthquakes.
How BranchPattern can help?
BranchPattern has expertise in enclosure consulting, green building certifications, building performance management, and ESG ratings. Our inter-disciplinary team efficiently evaluates design options across multiple criteria, reducing risk while increasing value. We strive to understand our customers’ needs and design services to achieve desired outcomes.
At BranchPattern, we are committed to sustainable development for industrial real estate. By emphasizing value, adaptability, and resilience, we help our customers realize their portfolio goals. For more information, please contact Stuart Shell, Lead Building Scientist at BranchPattern.
View More Resources
Benefit from our expertise
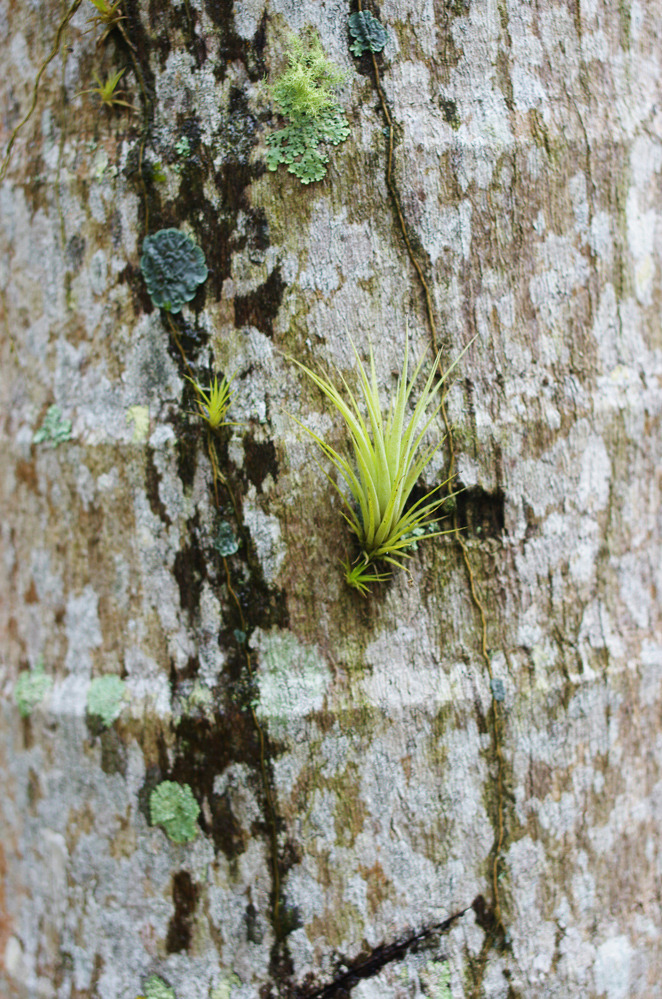
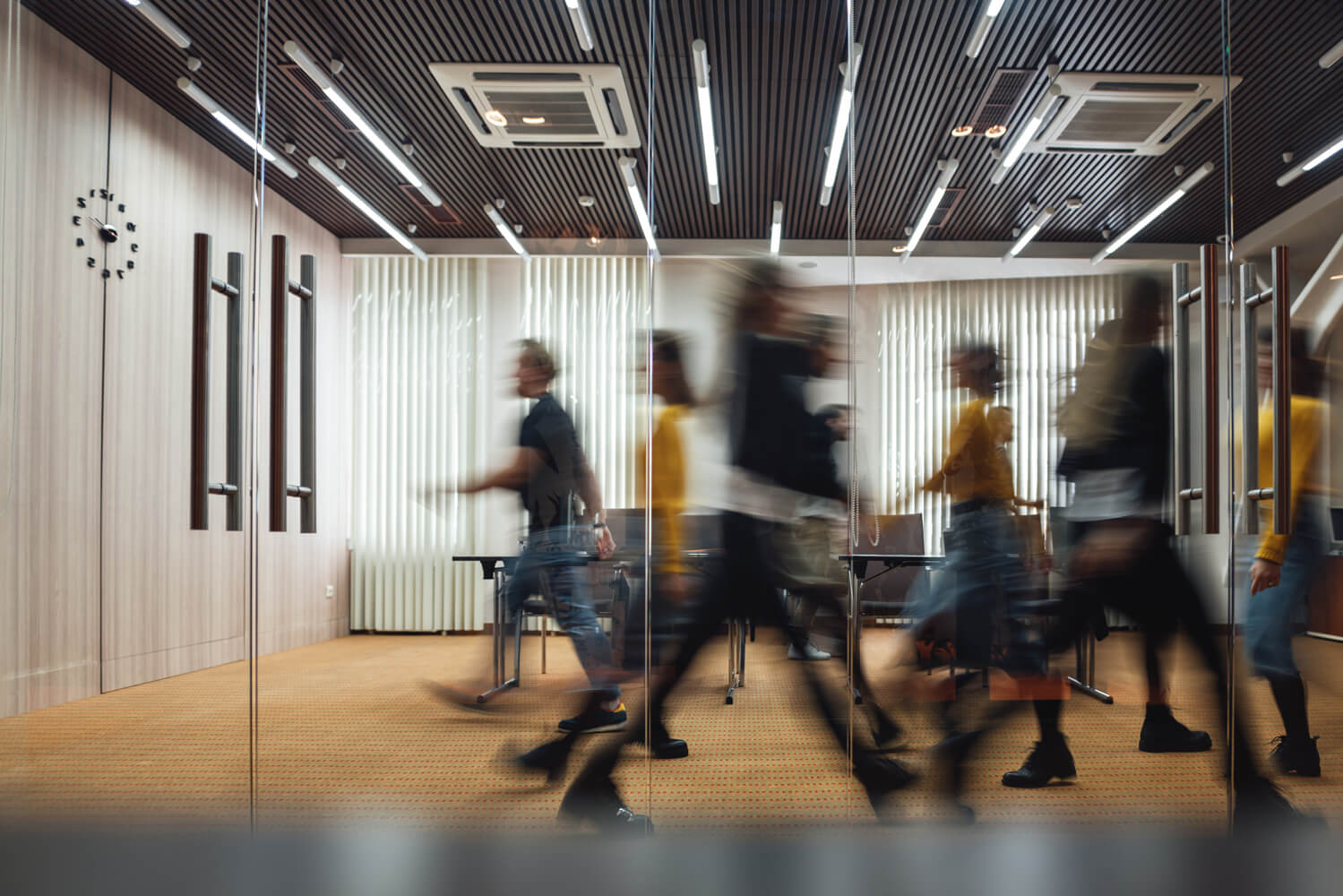