Reshoring the Rust Belt (Part 2 of 4)
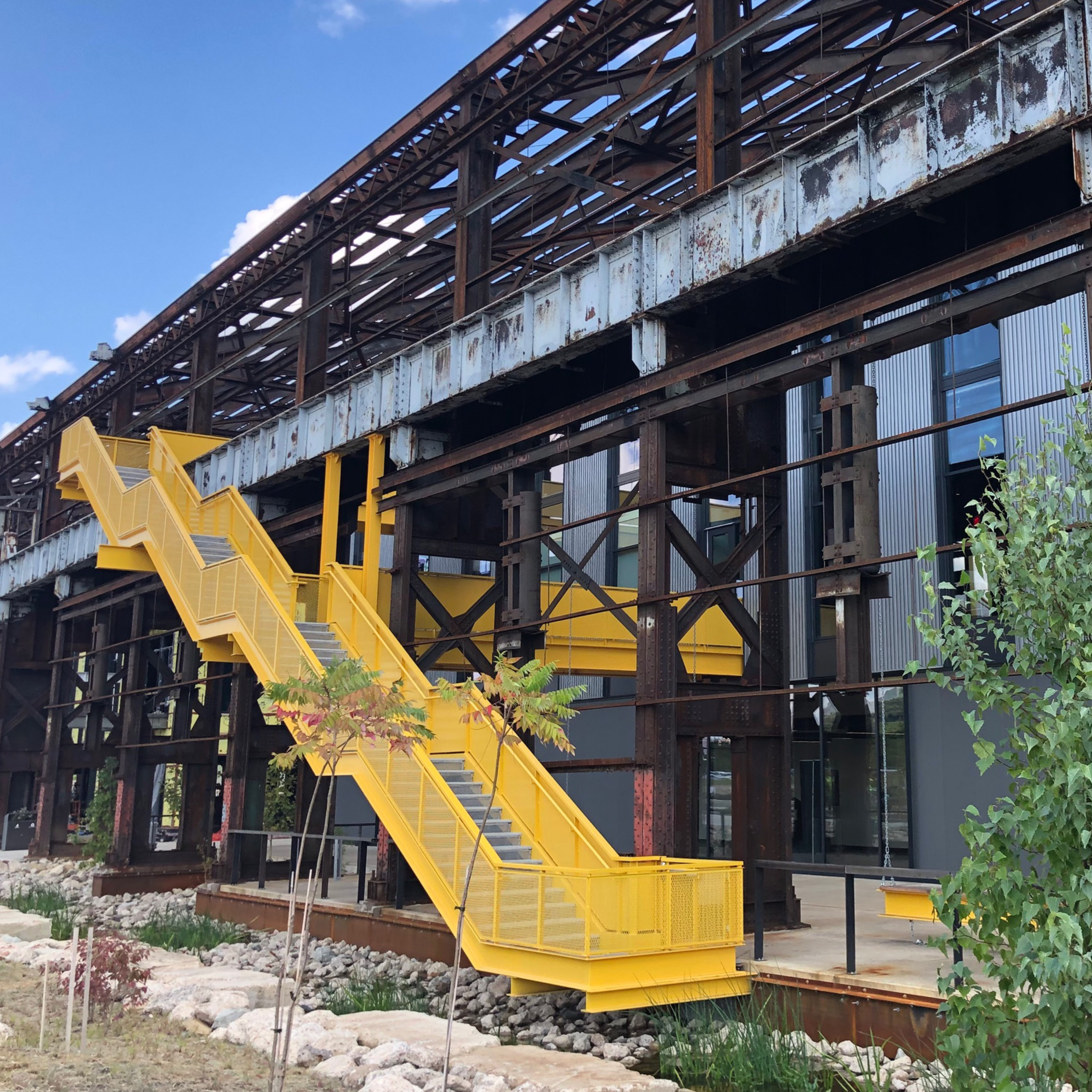
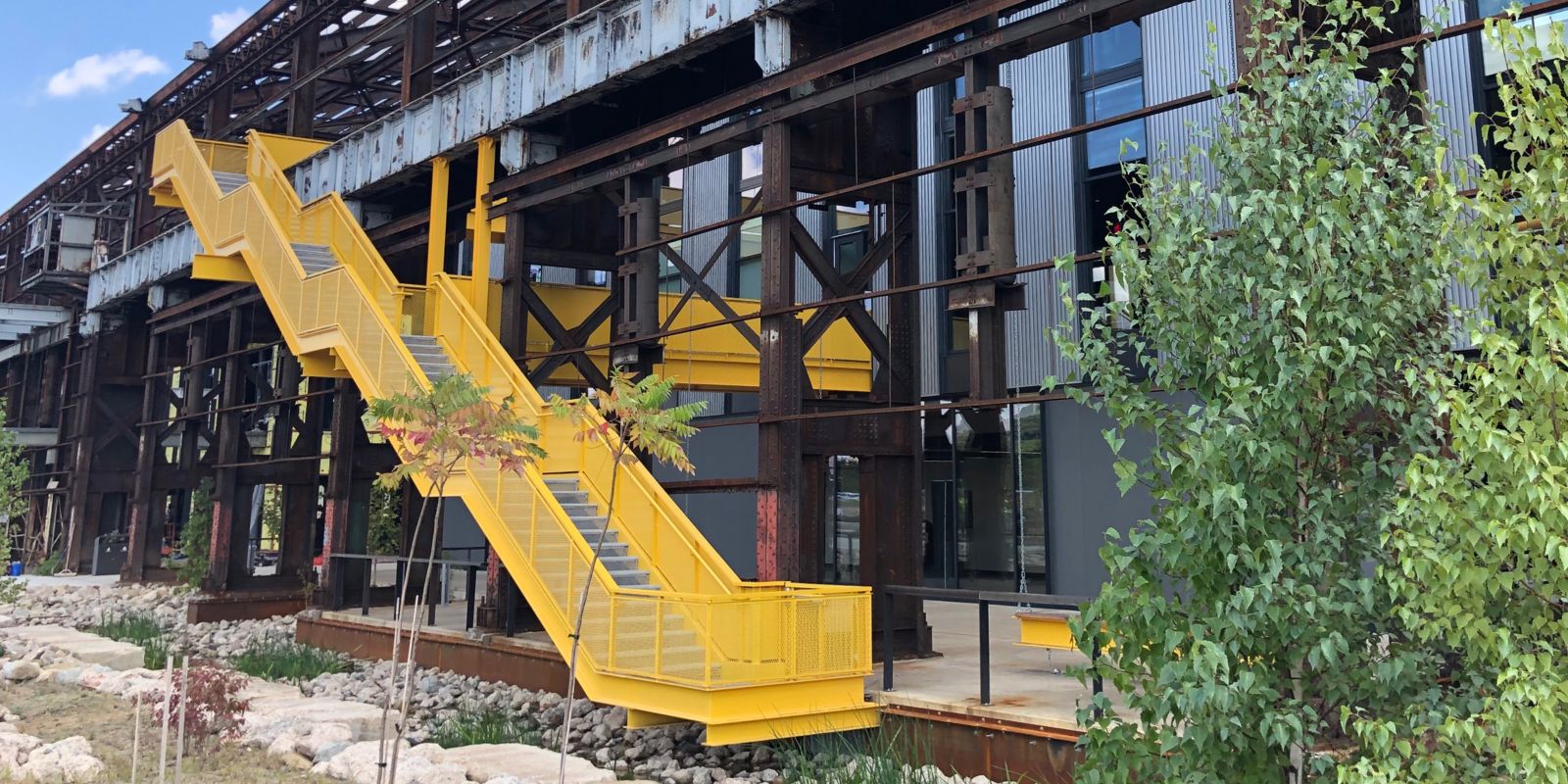
The Hidden Value in America's Manufacturing Legacy
Standing at the Point in downtown Pittsburgh, where three rivers converge, you can't help but feel the weight of history. The waters that once carried barges laden with steel now reflect a different skyline — one where tech companies occupy former factories, and where urban farms flourish in the shadows of old industrial sites. Recent examples we’ve supported include The Assembly, a historic Ford vertical factory, and Mill 19, a steel mill superstructure that now supports advanced robotics research. It's a transformation that speaks to the resilience and adaptability of Steel City, and it's happening across the entire Rust Belt.
The Architecture of Industry: Built to Last
The industrial architecture of the late 19th and early 20thcenturies wasn't just functional — it was a masterclass in sustainable design principles that we're only now beginning to fully appreciate. Take the Michigan Central Terminal in Detroit: its limestone facade, quarried from Indiana, represents not just materials but the embodied energy of extraction, transportation, and the skilled labor of countless stonemasons. The building's Beaux-Arts detailing isn't mere ornamentation — it's a testament to craftsmanship that would be prohibitively expensive to replicate today.
Natural Systems by Design
These industrial-era buildings incorporated sophisticated environmental strategies that we often miss at first glance:
- Daylight Design: The iconic sawtooth roofs of manufacturing facilities weren't just architectural flourishes – they were precisely engineered to provide consistent north light for workers while avoiding direct glare and solar heat gain.
- Stack Effect Ventilation: Multi-story industrial buildings typically featured operable clerestory windows and ventilation towers, creating natural air circulation that could move thousands of cubic feet of air per minute without mechanical assistance.
- Thermal Mass: Those thick masonry walls weren't just for show — they provided significant thermal inertia, helping to maintain stable interior temperatures through seasonal changes.
- Water Management: Many facilities incorporated sophisticated rainwater collection systems and used water features for process cooling – systems we're now reviving for modern sustainability goals.
The Carbon Equation: Numbers that Matter
When we examine buildings like Michigan Central Terminal or Pittsburgh's Strip District warehouses, the embodied carbon numbers are staggering:
- A typical pre-1940 industrial building contains 150-200 kg of embodied CO2 per square meter in its structure alone.
- The high-lime mortar used in historic masonry actually absorbs CO2 over time through carbonation.
- Replacing these structures with new construction would require an additional 500-700 kg of CO2 per square meter for new materials.
The Craftsmanship Factor
Modern construction methods can't easily replicate the durability of these structures:
- Hand-laid brick with lime mortar can last centuries and allows for natural building movement.
- Steel members from this era were often overengineered by today's standards, providing additional structural capacity for modern adaptations.
- Original growth timber used in these buildings has density and strength characteristics that are simply unavailable in modern lumber.
Building Performance: Old Meets New
These buildings present unique opportunities for high-performance retrofits:
- Envelope Performance: Thick masonry walls can be carefully retrofitted with interior insulation while maintaining their ability to manage moisture.
- Natural Ventilation: Original ventilation strategies can be augmented with modern controls to create hybrid systems that significantly reduce energy use.
- Daylighting: Historic window patterns and clerestories can be upgraded with high-performance glazing while maintaining their original function.
- Thermal Storage: The thermal mass of these structures can be actively incorporated into modern HVAC strategies, reducing peak loads and energy consumption.
The Technical Challenge: Engineering for Tomorrow
Adapting these buildings requires deep technical understanding:
- Envelope Analysis: Using hygrothermal modeling to ensure that modern interventions don't compromise historic masonry.
- Systems Integration: Threading modern mechanical and electrical systems through historic structures while preserving architectural integrity.
- Performance Monitoring: Implementing sophisticated monitoring to optimize building performance while protecting historic fabric.
Looking Forward: The Future of Our Industrial Heritage
As building performance professionals based in Pittsburgh, we understand that our industrial past isn't just history – it's a repository of embodied carbon, craftsmanship, and architectural wisdom. Every time we preserve and adapt an industrial building, we're leveraging century-old sustainable design strategies while adding modern technologies to create high-performance buildings for the future.
The Rust Belt cities aren't relics of a bygone era. They're laboratories for sustainable urban development, showing the world how to honor history while building for tomorrow. Through adaptive reuse, we're proving that the most sustainable building is often the one that's already standing.
For those involved in building design, construction, and management: the next time you see an old industrial building, don't see it as a liability. Instead, see it as an opportunity to create something extraordinary– a chance to build a resilient future while preserving the character of our cities.
Up next in Reshoring the Rust Belt: Part 3 outlines how existing buildings create a competitive advantage for post-industrial cities through the lens of environmental, social, and governance (ESG) performance.
View More Resources
Benefit from our expertise
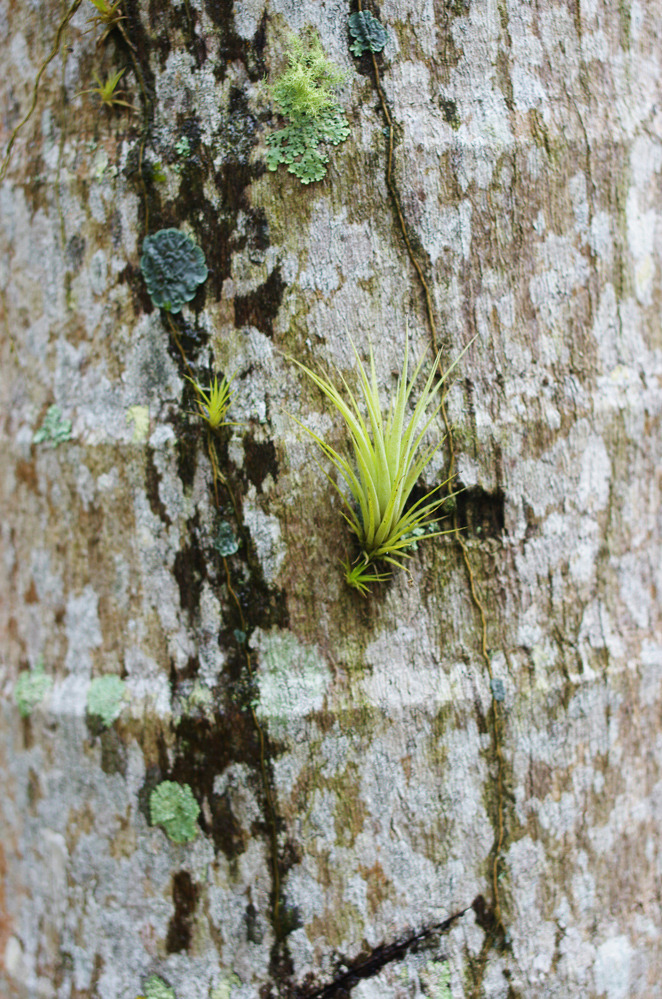
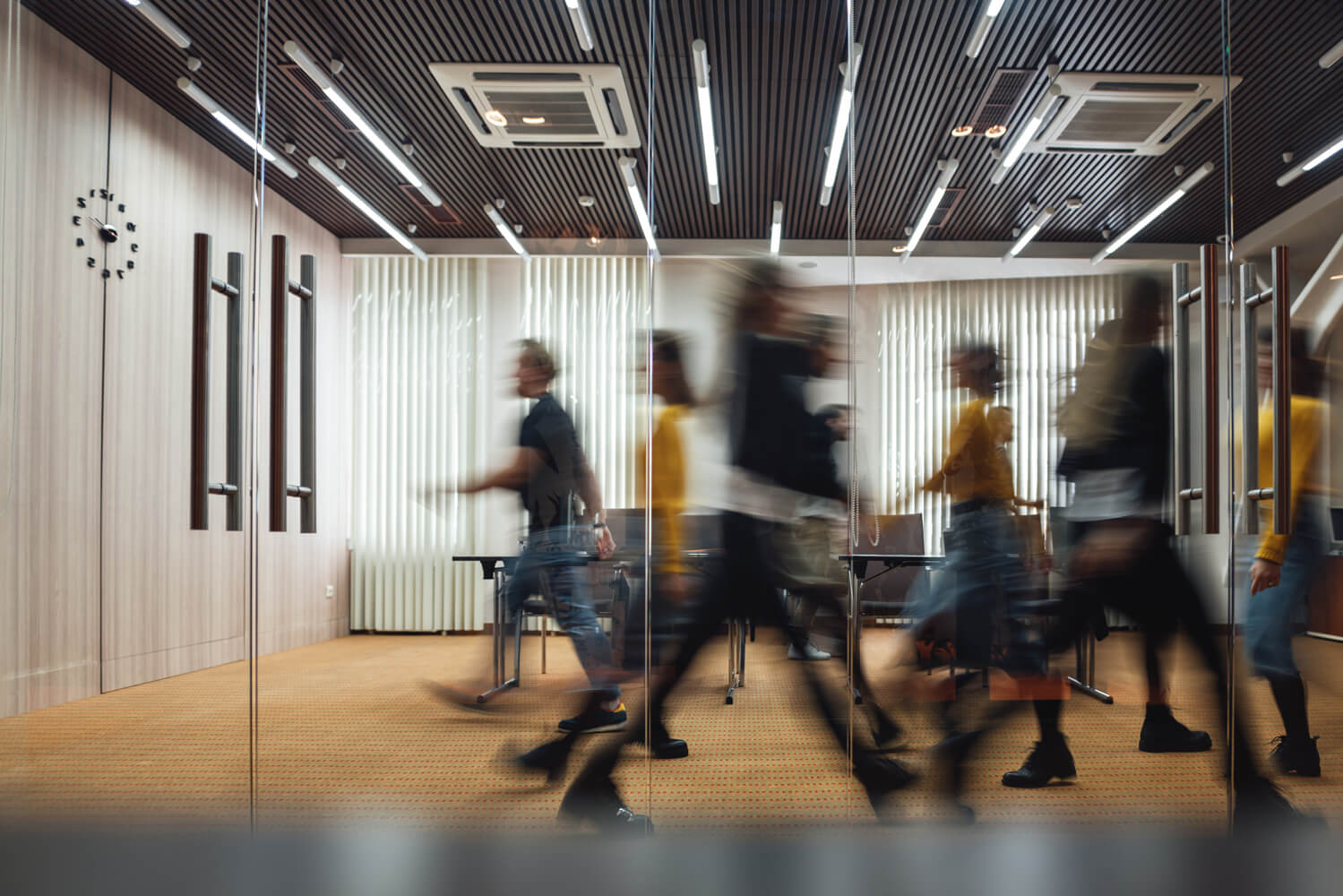